Ambr® Crossflow DF1, DF2 and Feed Bottle Kit
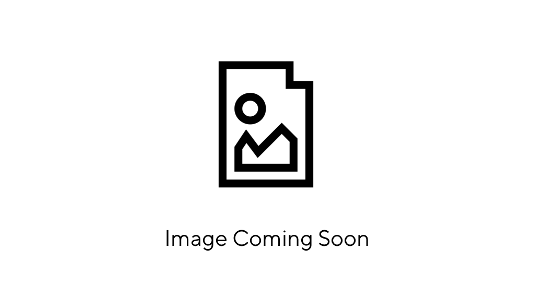
The Ambr® Crossflow DF1, DF2 and Feed Bottle Kit contains:
- 2 x 500ml glass bottles with caps, breathers and tubing assemblies for one channel
- 1 x 100ml glass bottle with caps, breathers and tubing assemblies for one channel
- Item No.:
- 061-2A33
- Piece
- 1
*Custom/bulk order quotes are provided within 72 hours of request.
About the Ambr® Crossflow System
Ambr® Crossflow is a benchtop crossflow system optimised for ultrafiltration and diafiltration applications. It is a small scale screening system with a minimum recirculation volume of 5 mL and a dedicated new range of Ambr® CF filter cassettes with 10 cm² membrane area.
Parallel operation is achieved with 4 independent crossflow channels per module, with up to 4 modules managed by one control station. This means Ambr® Crossflow is capable of performing membrane screenings with up to 16 Ambr® CF filters simultaneously.
Intuitive hardware and software design ensures that the system is quick to set up and easy to use, while full system automation ensures reliable process control and reduced manual intervention.
A small scale, high throughput automated system enables greater number of molecule | buffer combinations and process control conditions to be investigated. As a result early stage R&D productivity and efficiency will be improved significantly while costs per experiment are reduced.